Understanding Injection Mold Tools: A Comprehensive Guide
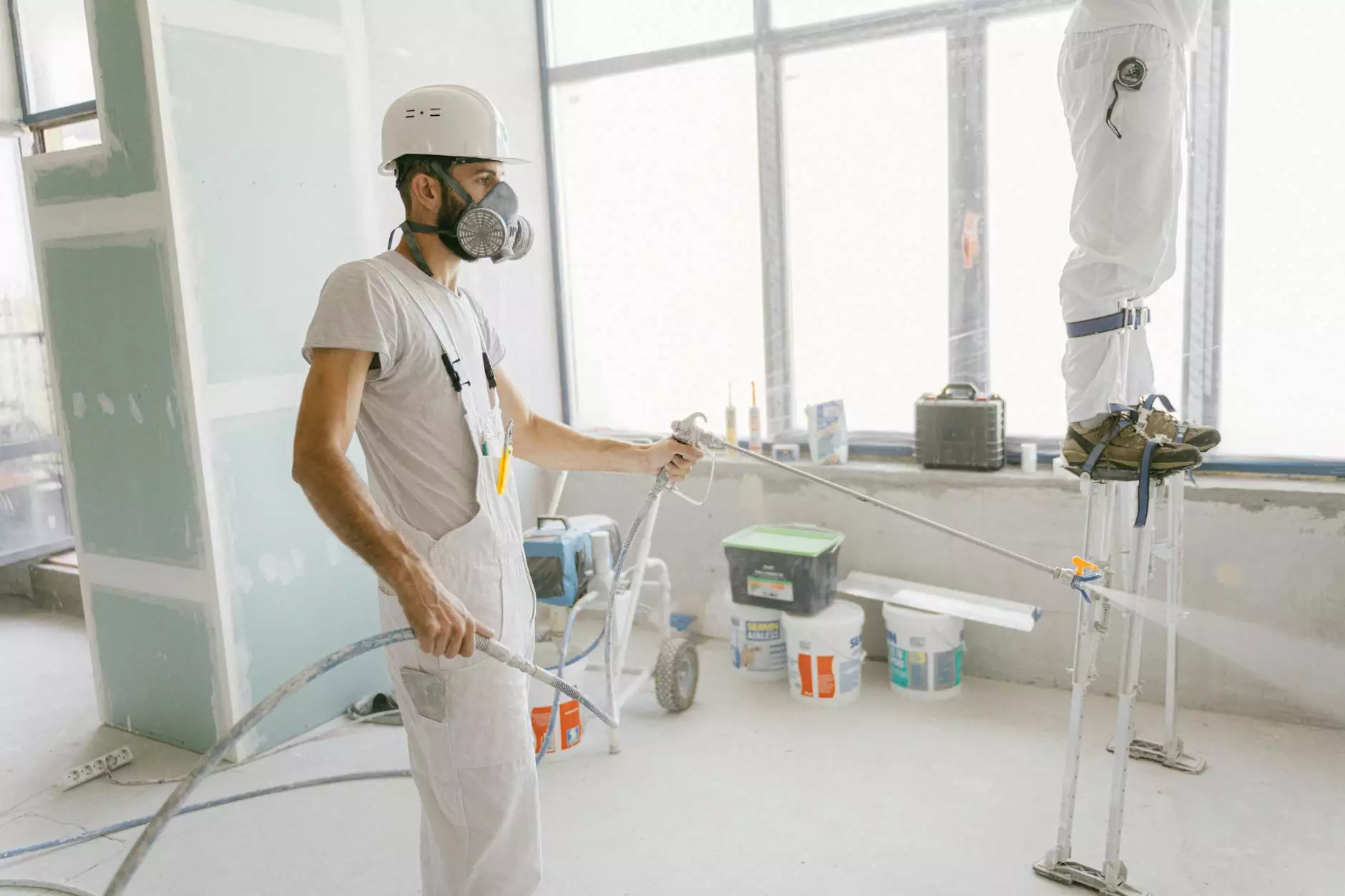
In the competitive realm of manufacturing, injection mold tools stand out as critical components that drive the efficiency and quality of production. This article will explore the intricacies of injection molding tools, their types, benefits, and how they play a significant role in metal fabrication, specifically in the context of deepmould.net.
What Are Injection Mold Tools?
Injection mold tools are specialized tools used in the manufacturing industry to produce a vast array of products through the injection molding process. This process involves injecting molten material into a mold, which then cools and solidifies to form specific shapes. The precision and quality of the end product largely depend on the design and quality of the injection mold tools utilized.
Components of Injection Mold Tools
The major components of injection mold tools include:
- Core and Cavity: The core is the inner part of the mold that defines the product's interior shape, while the cavity form the outer shape.
- Mold Base: This is the structure that supports the core and cavity, providing stability during the molding process.
- Cooling System: Efficient cooling systems are critical to reduce cycle times. They help manage the temperature of the mold during the injection process.
- Ejector Pins: After the molded part cools, it needs to be ejected from the mold. Ejector pins perform this task.
- Runner and Gate System: This is the pathway through which the molten material flows into the mold. It is crucial for ensuring consistent material distribution.
Types of Injection Mold Tools
There are several types of injection mold tools, each serving different manufacturing needs:
1. Single Cavity Molds
Single cavity molds produce one part per cycle. They are simpler and often used for lower production volumes or unique parts.
2. Multi-Cavity Molds
These molds contain multiple cavities, allowing for the production of several parts in one cycle. This type significantly boosts productivity and is ideal for mass production.
3. Family Molds
Family molds hold different parts in a single mold cavity, allowing for various components from a single injection cycle. This is particularly useful for related components.
4. Hot Runner Molds
This type features a heating system that keeps the plastic material molten as it travels through the runner, reducing waste and improving cycle time.
5. Cold Runner Molds
In cold runner molds, the material solidifies in the runner system, which can lead to waste. However, they are often easier to maintain and less expensive.
The Advantages of Injection Molding
The use of injection mold tools comes with several significant advantages that make them preferred in various manufacturing sectors:
- Efficiency: Injection molding is a highly efficient process, allowing for rapid production cycles.
- Precision: These tools can produce parts with very tight tolerances, a necessary feature in many industries.
- Material Versatility: A wide range of materials can be used in injection molding, including thermoplastics and thermosetting plastics.
- Low Labor Costs: Once the mold is designed and optimized, the production process requires less manual labor.
- Reduced Waste: The precision of injection molding minimizes material waste, contributing to more sustainable manufacturing practices.
The Manufacturing Process of Injection Mold Tools
Understanding the process of manufacturing injection mold tools is essential for appreciating their role in the production environment:
Step 1: Design and Engineering
The first and foremost step is designing the mold. Advanced CAD software plays a vital role in creating accurate designs that cater to the desired specifications of the product.
Step 2: Material Selection
Choosing the right materials for the mold itself is crucial. Steel and aluminum are commonly used, as they offer durability and resistance to wear.
Step 3: Machining
The selected materials are then machined to precision using CNC machining tools. This stage ensures that all components, including the core, cavity, and runner system, meet the design specifications.
Step 4: Assembly
After machining, the components are assembled together, ensuring that all parts fit correctly and function smoothly.
Step 5: Testing
Before mass production, the mold undergoes rigorous testing to ensure that it operates as expected. This includes trial runs and adjustments to optimize performance.
Step 6: Production
Once testing is complete, the mold is ready for full-scale production, enabling the manufacturer to create hundreds or thousands of identical parts efficiently.
Applications of Injection Mold Tools in Metal Fabrication
In the realm of metal fabrication, injection mold tools play an increasingly critical role:
- Automotive Components: Injection molding is widely used to produce complex components in the automotive industry, such as dashboards and interior fittings.
- Consumer Electronics: Many electronic devices rely on molded plastic parts for enclosures and internal components.
- Medical Devices: Precision parts for medical devices often utilize injection molding due to strict compliance and quality requirements.
- Packaging: Many packaging materials, including containers and caps, are manufactured using injection mold tools.
Future Trends in Injection Mold Tool Technology
The evolution of injection mold tools is ongoing, with several trends shaping their future:
1. Advanced Materials
Manufacturers are increasingly employing advanced materials like high-performance plastics and composites, offering enhanced strength and durability for molded products.
2. Automation and Smart Technologies
Automation is revolutionizing the injection molding process, reducing cycle times and improving consistency. The integration of AI and IoT technologies is leading to smart manufacturing practices.
3. Sustainability Initiatives
As industries push toward sustainability, manufacturers are prioritizing eco-friendly materials and processes that minimize waste and energy consumption during production.
4. Additive Manufacturing Integration
Combining additive manufacturing with injection molding allows for the rapid prototyping of molds, reducing lead times and costs in the design phase.
Conclusion
In conclusion, injection mold tools are indispensable in the manufacturing sector, especially within metal fabrication. Their ability to provide precision, efficiency, and versatility makes them a cornerstone of modern production. As industries continue to innovate and evolve, embracing advanced technologies and sustainable practices, the future of injection molding holds exciting possibilities. Whether you are in automotive, consumer electronics, or medical devices, understanding and utilizing high-quality injection mold tools can significantly enhance production outcomes.
At deepmould.net, we are committed to providing the best injection mold tools tailored to meet your manufacturing needs, ensuring quality and efficiency every step of the way.